Implementing a Computerized Maintenance Management System (CMMS) is a strategic move that can revolutionize your maintenance operations, enhancing efficiency, reducing costs, and boosting productivity. However, a successful CMMS implementation requires careful planning, collaboration, and a well-defined roadmap. In this comprehensive guide, we will walk you through the essential steps to effectively implement a CMMS.
Step 1: Define Clear Objectives
Before diving into the implementation process, it’s crucial to clearly define your organization’s objectives and goals. Are you aiming to reduce downtime, improve maintenance scheduling, optimize inventory management, or enhance compliance? Identifying these goals upfront will provide a roadmap for your CMMS implementation strategy and help align your efforts with the outcomes.
Step 2: Select the Right CMMS Software
Selecting the appropriate CMMS software is a critical decision. Research various options based on your organization’s size, industry, and specific requirements. Look for features such as work order management, preventive maintenance scheduling, inventory tracking, reporting, and user-friendly interfaces. Scalability and integration capabilities are also important factors to consider, as they ensure that the CMMS can grow with your organization and seamlessly integrate with existing systems.
Step 3: Assemble a Cross-Functional Team
Effective CMMS implementation requires collaboration across various departments. Create a cross-functional team that includes representatives from maintenance, IT, operations, and any other relevant areas. Assign roles and responsibilities to team members, ensuring that each person understands their contribution to the implementation process.
Step 4: Data Preparation and Cleaning
Accurate data is the foundation of successful CMMS implementation. Gather and organize your maintenance-related data, including equipment details, maintenance history, and inventory. Clean and validate the data to ensure its accuracy, which will facilitate a smooth transition into the new system.
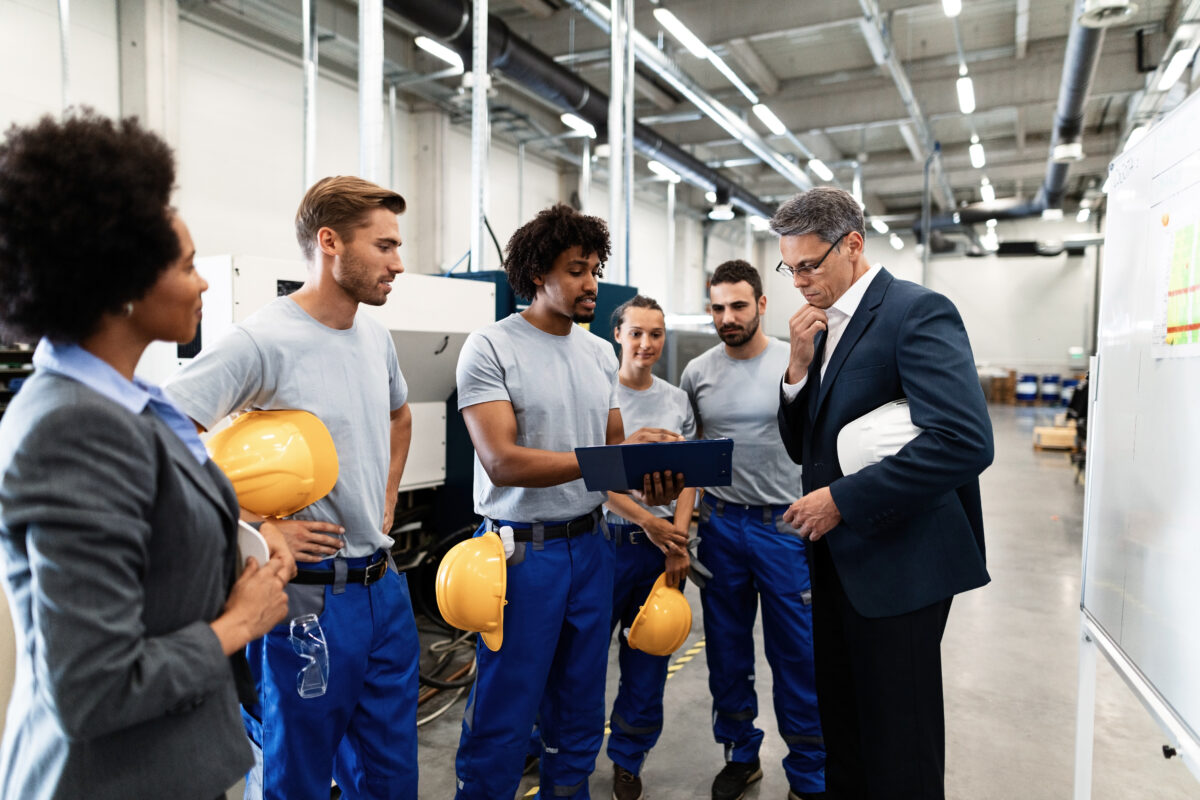
Step 5: Customize and Configure
Tailor the CMMS to fit your organization’s unique processes and workflows. Customize fields, forms, and reports to capture the specific information needed for your maintenance operations. This step ensures that the CMMS aligns seamlessly with your existing practices.
Step 6: Comprehensive Training
Provide comprehensive training to all users who will interact with the CMMS. From maintenance technicians to supervisors, everyone should receive hands-on training to effectively navigate the system, input data, and generate reports. Investing time in training will pay off by maximizing user adoption and system utilization.
Step 7: Pilot Testing
Before rolling out the CMMS to the entire organization, conduct a pilot test with a small group of users. This phase allows you to identify any issues or challenges early on and gather valuable feedback from users who are directly engaging with the system. Use this feedback to refine and improve the CMMS configuration.
Step 8: Data Migration
Transfer your existing maintenance data into the CMMS, ensuring that the data is accurately imported and validated. This step preserves historical information and enables you to leverage the CMMS’s capabilities from day one.
Step 9: Integration with Existing Systems
If applicable, integrate the CMMS with other systems your organization uses, such as ERP software, asset management platforms, or IoT sensors. Integration enhances data exchange and ensures a cohesive technological ecosystem.
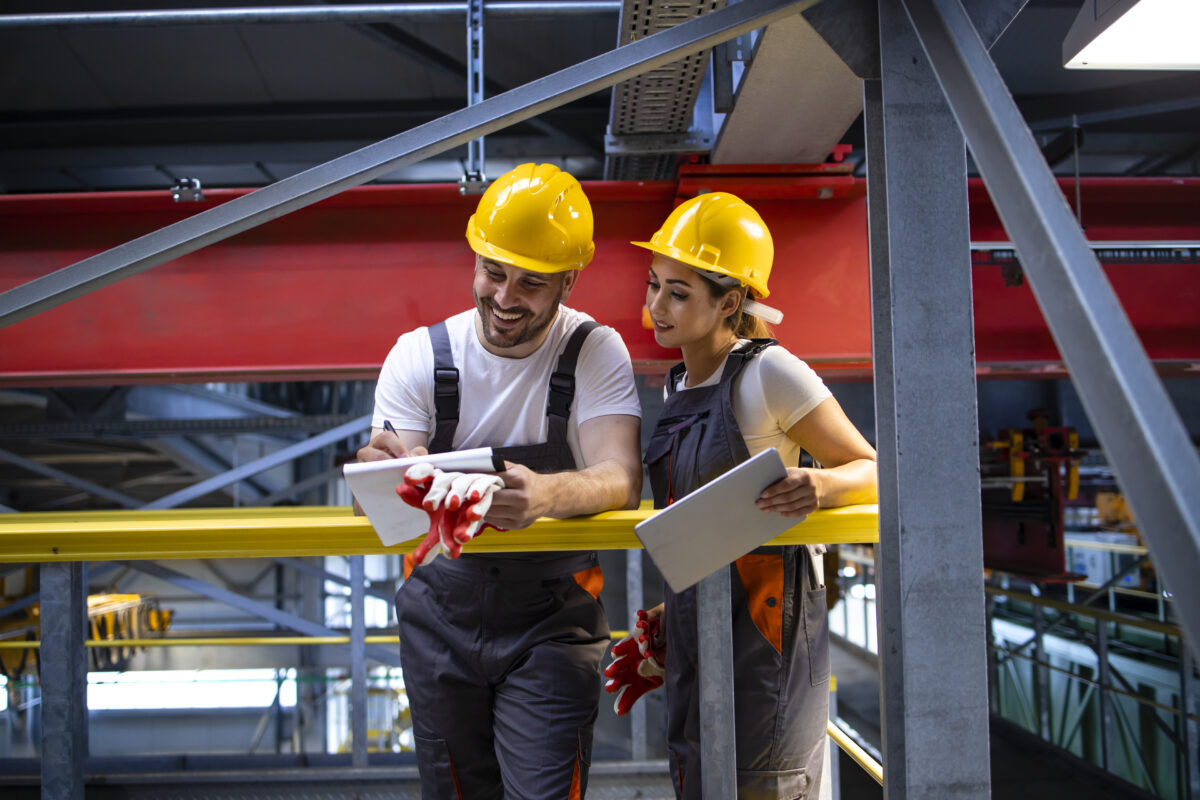
Step 10: Change Management and Communication
Communicate the benefits of the CMMS to all stakeholders within your organization. Address any concerns or resistance to change by highlighting how the system will improve processes, increase efficiency, and contribute to the organization’s success.
Step 11: Go-Live and Continuous Improvement
With the necessary training, testing, and integration in place, it’s time to roll out the CMMS across your organization. Monitor its usage and performance closely during the initial period, collecting feedback and making necessary adjustments to optimize its effectiveness.
Step 12: Performance Measurement and KPIs
Establish key performance indicators (KPIs) to measure the impact of the CMMS on various aspects of maintenance operations. Monitor metrics such as downtime reduction, increased asset reliability, improved inventory management, and cost savings.
Step 13: Ongoing Training and Support
Provide ongoing training and support to users as needed. Maintain open communication channels for users to report issues, suggest improvements, and seek assistance when using the CMMS.
Step 14: Continuous Optimization
Regularly review and analyze the data generated by the CMMS to identify opportunities for improvement. Use data-driven insights to refine maintenance strategies, optimize workflows, and enhance overall operational efficiency.